The Plate and Shell detachable version heat exchanger offers increased flexibility of use by allowing the fully welded plate pack to be completely withdrawn from the shell for inspection or cleaning. This is achieved by the use of a flanged and bolted shell construction. The cassette-type plate pack allows quick and easy removal and refitting thus ensuring that process downtime is kept to a minimum.
Key Features of the Plate and Shell Heat Exchanger
- Bolted shell construction allows removal of plate pack
- Fully welded on plate side of the unit
- The area required for plate pack removal is considerably smaller than for shell and tube bundle
- Design pressure up to 100 bar
- Standard design temperature -80°C to +400°C higher for special cases
- Very compact – 300m² heat transfer area / m²
- Capacity up to 100MW / unit with up to 1800m² / unit
- Significant space saving & weight compared to tubular units
- Economic to maintain – very quick to open and gaskets to replace
Applications:
- Liquid/ liquid processing
- Condensers
- Evaporators
- Cascades
- Fouling service
- Gas/ Liquid
- Plate and Shell Heat Exchangers (PSHE) have been developed over recent years to bridge the performance and price gaps between the traditional Shell and Tube and the higher thermally efficient gasket Plate type Heat Exchanger (PHE).
- The aim is to extend the range of the successful Plate Heat Exchanger while removing the temperature and pressure limitations.
- High thermal efficiency can now be enjoyed from – 200 to 350 degrees C and pressures up to 100bar.
- Plate and Shell heat exchangers consist of a series of corrugated plates welded on alternative ends, without peripheral gaskets.
- The welded plate pack is inserted and either welded or bolted within a steel frame. All liquid contact surfaces are manufactured in stainless steel that eliminates corrosion due to aggressive media. If stainless steel is not suitable other higher grade materials are available, such as Titanium, 245 SMO, or Nickel.
- Plate and Shell Heat Exchangers are Work Cover Approved and manufactured in an ISO
9001 quality approved manufacturing facility, to meet all international heat exchange
standards
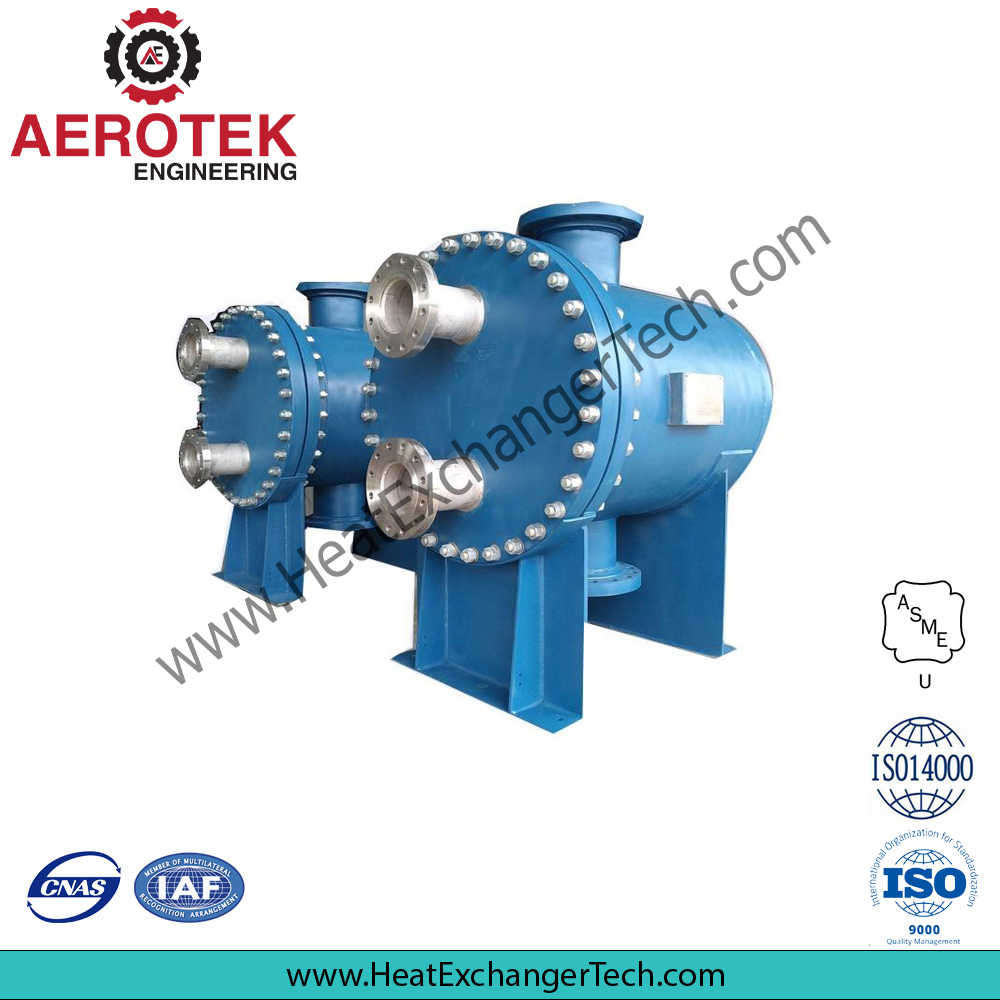
Send Inquiry